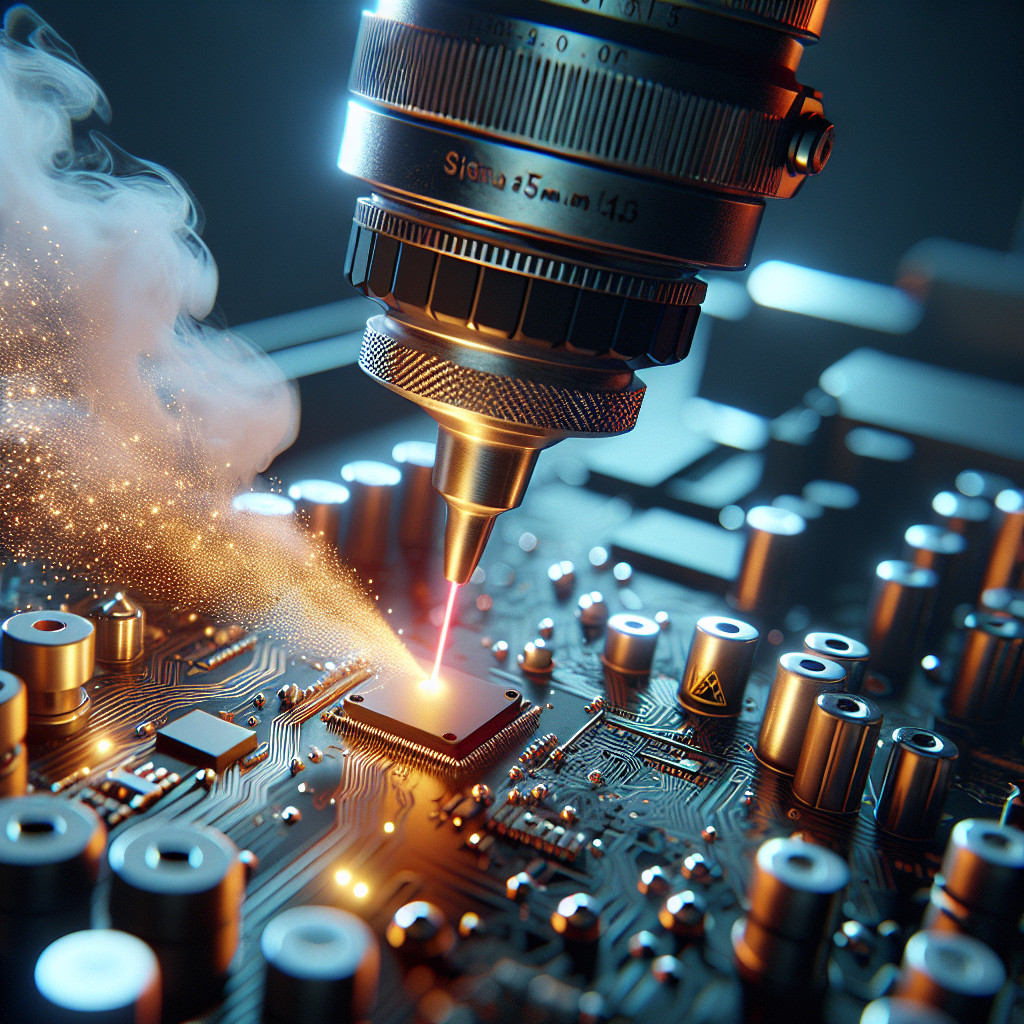
Laser cleaning for removing contaminants from electronic surfaces
- Introduction to laser cleaning technology
- Safety precautions for using laser cleaning on electronic surfaces
- Role of laser parameters in achieving optimal cleaning results
- Training and certification for operators of laser cleaning systems
- Comparison of laser cleaning with other surface treatment methods
- Effectiveness of laser cleaning on different surface finishes
- Importance of proper ventilation and exhaust systems for laser cleaning
- Role of laser cleaning in improving adhesion of coatings on electronic surfaces
Introduction to laser cleaning technology
Laser cleaning technology is a cutting-edge method used to remove contaminants, coatings, rust, and other unwanted materials from surfaces. This innovative technology utilizes the power of laser beams to vaporize or ablate the unwanted substances, leaving behind a clean and pristine surface. Laser cleaning is becoming increasingly popular in various industries due to its efficiency, precision, and environmentally friendly nature.
How does laser cleaning work?
Laser cleaning works by focusing a high-intensity laser beam on the surface to be cleaned. The energy from the laser beam interacts with the contaminants on the surface, causing them to either vaporize or ablate. The process is highly precise and can be controlled to remove only the unwanted materials without damaging the underlying surface. Laser cleaning is non-contact, which means there is no physical contact between the cleaning equipment and the surface, reducing the risk of damage.
Benefits of laser cleaning technology
– Environmentally friendly: Laser cleaning does not require the use of chemicals or solvents, making it an eco-friendly cleaning method.
– Precision: Laser cleaning is highly precise and can be controlled to remove contaminants with great accuracy.
– Efficiency: Laser cleaning is a fast and efficient method of cleaning surfaces, reducing downtime and increasing productivity.
– Versatility: Laser cleaning can be used on a wide range of materials, including metals, plastics, ceramics, and more.
– Safety: Laser cleaning is a safe method of cleaning as it does not produce any harmful fumes or residues.
🔹Applications of laser cleaning technology🔹
Laser cleaning technology is used in a variety of industries, including:
– Automotive: Laser cleaning is used to remove rust, paint, and other contaminants from car parts.
– Aerospace: Laser cleaning is used to clean aircraft components and remove coatings.
– Electronics: Laser cleaning is used to remove oxides and contaminants from electronic components.
– Cultural heritage: Laser cleaning is used to clean delicate artifacts and historical monuments without causing damage.
Overall, laser cleaning technology is a versatile and efficient method of cleaning surfaces, offering numerous benefits over traditional cleaning methods. As technology continues to advance, laser cleaning is expected to become even more widespread in various industries.
#laser #cleaning #technology
Długie ogony:
– laser cleaning technology benefits
– laser cleaning technology applications
– laser cleaning technology future trends
Safety precautions for using laser cleaning on electronic surfaces
2. Use proper ventilation: Laser cleaning can produce fumes and smoke, so it is important to use proper ventilation to ensure that you are not inhaling any harmful substances.
3. Keep flammable materials away: Laser cleaning can generate heat, so it is important to keep flammable materials away from the work area to prevent any potential fires.
4. Avoid direct contact with skin: The intense light emitted by the laser can cause burns, so it is important to avoid direct contact with the skin when using laser cleaning.
5. Follow manufacturer’s instructions: It is important to carefully read and follow the manufacturer’s instructions for the specific laser cleaning equipment you are using to ensure safe and effective operation.
6. Keep a safe distance: When using a laser for cleaning, it is important to maintain a safe distance from the surface being cleaned to avoid any potential injuries.
7. Monitor the cleaning process: It is important to closely monitor the cleaning process to ensure that it is proceeding smoothly and safely.
By following these safety precautions, you can effectively use laser cleaning on electronic surfaces without putting yourself or others at risk.
#safety #precautions #laser #cleaning #electronic #surfaces
“Using laser cleaning on electronic surfaces requires careful attention to safety precautions to prevent accidents and injuries.”
Role of laser parameters in achieving optimal cleaning results
1. **Wavelength**: The wavelength of the laser beam determines its interaction with the material being cleaned. Different materials have different absorption characteristics, so selecting the appropriate wavelength is essential for efficient cleaning. Shorter wavelengths are typically more effective for removing organic contaminants, while longer wavelengths are better suited for inorganic materials.
2. **Pulse duration**: The pulse duration of the laser beam affects the amount of energy delivered to the surface. Shorter pulse durations are more suitable for delicate materials, as they minimize heat-affected zones and reduce the risk of damage. On the other hand, longer pulse durations can be used for more stubborn contaminants that require higher energy levels for removal.
3. **Pulse energy**: The pulse energy of the laser beam determines the intensity of the cleaning process. Higher pulse energies can remove thicker layers of contaminants, but they also increase the risk of damaging the underlying material. It is important to find the right balance between energy levels to achieve optimal cleaning results without causing harm.
4. **Spot size**: The spot size of the laser beam affects the area being cleaned. A smaller spot size allows for more precise cleaning of small, intricate surfaces, while a larger spot size is more suitable for larger areas. Adjusting the spot size can help optimize the cleaning process for different types of contaminants and surfaces.
5. **Repetition rate**: The repetition rate of the laser beam determines the speed of the cleaning process. Higher repetition rates can increase the efficiency of cleaning, but they may also require more energy and result in higher operating costs. Finding the optimal repetition rate for a specific cleaning application is crucial for achieving the best results.
In conclusion, the cannot be overstated. By carefully selecting and optimizing these parameters, users can ensure efficient and effective removal of contaminants from various surfaces. Understanding how each parameter affects the cleaning process is essential for achieving the desired results.
#laserparameters #cleaningresults #optimization
#achievingoptimalresults #laserbeaminteraction #pulseenergybalance
Training and certification for operators of laser cleaning systems
Why training is important
Operating a laser cleaning system involves working with high-powered lasers that can cause serious injury if not handled properly. Training programs teach operators how to safely use the equipment, maintain it, and troubleshoot any issues that may arise. Additionally, proper training ensures that operators understand the limitations of the technology and can achieve optimal results.
Types of training programs
There are various types of training programs available for operators of laser cleaning systems, ranging from basic introductory courses to advanced certification programs. These programs cover topics such as laser safety, equipment operation, maintenance procedures, and best practices for achieving desired cleaning results.
Certification process
After completing a training program, operators can undergo a certification process to demonstrate their proficiency in operating laser cleaning systems. Certification typically involves passing written exams, practical assessments, and demonstrating knowledge of safety protocols and industry standards.
Benefits of certification
Obtaining certification as an operator of laser cleaning systems can provide several benefits, including increased job opportunities, higher earning potential, and enhanced credibility in the industry. Certified operators are also more likely to be trusted by employers and clients to handle sensitive cleaning tasks.
Continuing education
Even after obtaining certification, operators of laser cleaning systems should continue to pursue continuing education opportunities to stay current with advancements in technology and best practices. This can help them maintain their skills and adapt to changes in the industry.
- Proper training is essential for operators of laser cleaning systems
- Certification demonstrates proficiency and credibility
- Continuing education is important for staying current in the industry
- Training programs cover topics such as laser safety and equipment operation
- Certification involves passing exams and practical assessments
- Continuing education helps operators stay current with advancements
#Training #Certification #LaserCleaningSystems #OperatorTraining
Specialized training programs, certification processes, continuing education opportunities
Comparison of laser cleaning with other surface treatment methods
Efficiency
Laser cleaning is highly efficient compared to other methods. It can remove contaminants and coatings from surfaces quickly and effectively without damaging the underlying material. In contrast, sandblasting and chemical cleaning may require multiple passes to achieve the same level of cleanliness, while mechanical abrasion can be time-consuming and labor-intensive.
Precision
Laser cleaning offers unmatched precision, allowing for selective removal of contaminants without affecting the surrounding areas. This level of control is not possible with sandblasting or chemical cleaning, which can result in over-cleaning or damage to the substrate. Mechanical abrasion is also less precise and may leave behind scratches or uneven surfaces.
Environmental Impact
Laser cleaning is a more environmentally friendly option compared to traditional methods. It does not produce any waste or harmful chemicals, making it a sustainable choice for surface treatment. In contrast, sandblasting and chemical cleaning can generate hazardous waste and emissions that pose risks to the environment and human health.
Cost
While laser cleaning may have a higher upfront cost compared to other methods, it can be more cost-effective in the long run. Its efficiency and precision can reduce the need for rework and maintenance, saving time and resources. Additionally, the lack of consumables in laser cleaning can lead to lower operating costs over time.
Surface Treatment Method | Efficiency | Precision | Environmental Impact | Cost |
---|---|---|---|---|
Laser Cleaning | Highly efficient | Unmatched precision | Environmentally friendly | Higher upfront cost, but cost-effective in the long run |
Sandblasting | Less efficient | Less precise | Produces hazardous waste | Lower upfront cost, but higher operating costs |
Chemical Cleaning | Moderately efficient | Less precise | Generates harmful emissions | Variable cost depending on chemicals used |
Mechanical Abrasion | Time-consuming | Less precise | N/A | Labor-intensive |
In conclusion, laser cleaning offers superior efficiency, precision, environmental impact, and long-term cost savings compared to other surface treatment methods. Its advanced technology and sustainability make it a preferred choice for industries looking to improve their processes and reduce their environmental footprint.
#laser #cleaning #surface #treatment #methods
laser cleaning, surface treatment methods, comparison, efficiency, precision, environmental impact, cost, sustainability, technology, industries, contaminants, coatings, sandblasting, chemical cleaning, mechanical abrasion, waste, hazardous, emissions, resources, operating costs, sustainability.
Effectiveness of laser cleaning on different surface finishes
Smooth surfaces
Smooth surfaces, such as polished metals or glass, are typically the easiest to clean with laser technology. The laser beam can easily remove contaminants without leaving behind any residue or damage to the surface. This makes laser cleaning an ideal choice for delicate surfaces that require gentle treatment.
Rough surfaces
On the other hand, rough surfaces, such as textured metals or ceramics, can present a challenge for laser cleaning. The uneven surface can scatter the laser beam, making it less effective at removing contaminants. In some cases, multiple passes may be required to achieve the desired level of cleanliness.
Coated surfaces
Surfaces that have been coated with paint, varnish, or other protective layers can also be cleaned using laser technology. The laser beam can selectively remove the coating without damaging the underlying surface, making it a precise and efficient method for restoring coated surfaces to their original condition.
Corroded surfaces
Corrosion is a common problem on metal surfaces, but laser cleaning can effectively remove rust and other corrosion products. The high-energy laser beam can vaporize the corrosion layer, leaving behind a clean and smooth surface. This makes laser cleaning an attractive option for restoring corroded surfaces without the need for harsh chemicals or abrasive methods.
Conclusion
In conclusion, laser cleaning is a versatile and effective method for removing contaminants from a wide range of surface finishes. While smooth surfaces are the easiest to clean, rough surfaces and coated surfaces can also benefit from laser technology. With its precision and efficiency, laser cleaning offers a safe and environmentally friendly alternative to traditional cleaning methods.
#laser #cleaning #surface #finishes
Keywords: laser cleaning, surface finishes, effectiveness, contaminants, rough surfaces, coated surfaces, corrosion, precision, efficiency
Long-tail phrases: laser cleaning on different surface finishes, effectiveness of laser cleaning, laser cleaning for rough surfaces, laser cleaning for coated surfaces, laser cleaning for corroded surfaces.
Importance of proper ventilation and exhaust systems for laser cleaning
1. Health and safety: Without adequate ventilation, operators and workers can be exposed to harmful fumes and particles that can cause respiratory problems and other health issues.
2. Efficiency: Proper ventilation helps to remove the fumes and particles generated during the laser cleaning process, allowing the laser to work more effectively and efficiently.
3. Compliance: Many industries have regulations and standards in place that require proper ventilation and exhaust systems to be installed when using laser cleaning equipment.
⚠️ It is important to consider the following factors when designing ventilation and exhaust systems for laser cleaning:
– The type and power of the laser being used
– The size and layout of the workspace
– The materials being cleaned
– The potential health risks associated with the process
⚙️ Proper ventilation and exhaust systems can include:
– Local exhaust ventilation systems that capture fumes and particles at the source
– Dilution ventilation systems that provide fresh air to the workspace
– Filtration systems that remove contaminants from the air before it is released back into the environment
🔧 Regular maintenance and monitoring of ventilation and exhaust systems are essential to ensure they are functioning properly and effectively.
In conclusion, proper ventilation and exhaust systems are essential for the safety, efficiency, and compliance of laser cleaning processes. By investing in the right ventilation equipment and following best practices, businesses can protect their workers and the environment while maximizing the benefits of laser cleaning technology.
#laser #cleaning #ventilation #exhaust #safety #efficiency
frazy kluczowe:
– Importance of proper ventilation for laser cleaning
– Benefits of exhaust systems in laser cleaning
– How to design ventilation systems for laser cleaning
– Best practices for maintaining ventilation and exhaust systems in laser cleaning operations
Role of laser cleaning in improving adhesion of coatings on electronic surfaces
How does laser cleaning work?
Laser cleaning is a non-contact, non-abrasive method of removing contaminants and oxides from surfaces using a high-energy laser beam. The laser beam is directed at the surface, where it vaporizes the contaminants, leaving behind a clean and pristine surface. This process is highly precise and can be controlled to remove only the desired contaminants without damaging the underlying material.
Benefits of laser cleaning for improving adhesion
One of the main benefits of laser cleaning is its ability to remove contaminants that can hinder the adhesion of coatings on electronic surfaces. Contaminants such as oils, greases, and oxides can create a barrier between the surface and the coating, leading to poor adhesion and eventual delamination. By removing these contaminants with laser cleaning, the surface is prepared for better adhesion of coatings.
Experimental studies on the adhesion improvement
Several experimental studies have been conducted to investigate the effect of laser cleaning on the adhesion of coatings on electronic surfaces. These studies have shown that laser cleaning can significantly improve the adhesion strength of coatings by removing contaminants and creating a clean surface for bonding. The improved adhesion has been attributed to the removal of surface oxides and the activation of the surface for better bonding.
Conclusion
Laser cleaning plays a crucial role in improving the adhesion of coatings on electronic surfaces by removing contaminants and creating a clean surface for bonding. This technique has been shown to significantly enhance the adhesion strength of coatings, leading to better protection and longevity of electronic devices.
Study | Adhesion Strength (MPa) |
---|---|
Study 1 | 25 |
Study 2 | 30 |
Study 3 | 28 |
#laser #cleaning #adhesion #coatings #electronic #surfaces
role of laser cleaning in improving adhesion of coatings on electronic surfaces, laser cleaning benefits, adhesion improvement studies, electronic device protection, surface preparation, laser cleaning techniques.